Wir helfen DIR indem wir flexibel alle Alternativen Herstellungsverfahren mit dir
evaluieren, damit dein Produkt zum Verkaufsschlager wird!
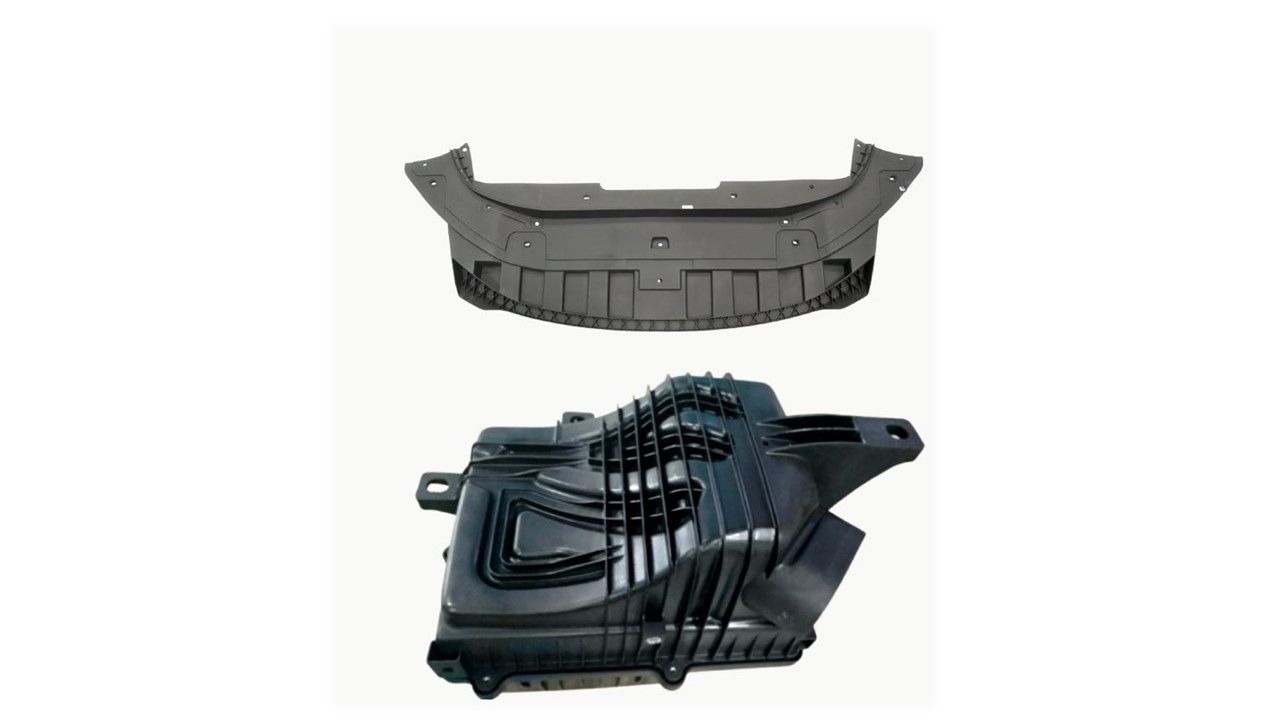
Es begann alles mit einem Produkt, das ursprünglich bei uns in PA2200 gebaut wurde. Die Stückzahlen erhöhten sich aber drastisch, sodass der Kunde hin-/hergerissen war ob es nicht doch in den Spritzguss gehen soll!
Spritzguss erschien zunächst als gute Option, doch dann stellte sich heraus, dass aufgrund der Hinterschnitte im Bauteil eine Herstellung im Spritzguss nicht möglich war. Dies stellte uns und den Kunden vor eine Herausforderung, da eine kostengünstige und flexible Lösung gefunden werden musste.
Nach gründlicher Analyse und Evaluierung verschiedener Optionen entschied sich das Team dafür, das Produkt für den Vakuumguss anzupassen. Der Vakuumguss ist ein Verfahren, bei dem ein Silikonwerkzeug verwendet wird, um das gewünschte Teil herzustellen. Dieser Prozess ermöglicht die Herstellung von Teilen mit komplexen Geometrien und Hinterschnitten, was für das Produkt unerlässlich war.
Die Anpassung des Produkts für den Vakuumguss erwies sich als äusserst erfolgreich. Nicht nur konnten die Hinterschnitte problemlos hergestellt werden, sondern auch die Kosten und die Flexibilität des Herstellungsprozesses verbesserten sich erheblich. Der Vakuumguss ermöglichte es, das Produkt in grossen Stückzahlen kostengünstig herzustellen, ohne dabei Kompromisse bei der Qualität einzugehen. Dank dieser Anpassung konnte das Produkt erfolgreich zum Serienteil werden. Dies führte zu einer höheren Kundenzufriedenheit und einem grösseren Markterfolg.
Diese Erfolgsstory zeigt, wie wichtig es ist, flexibel zu sein und alternative Herstellungsverfahren zu evaluieren, wenn Hindernisse auftreten. Durch die Anpassung des Produkts für den Vakuumguss konnte das Team eine innovative Lösung finden und das Produkt erfolgreich für den Kunden auf den Markt bringen.
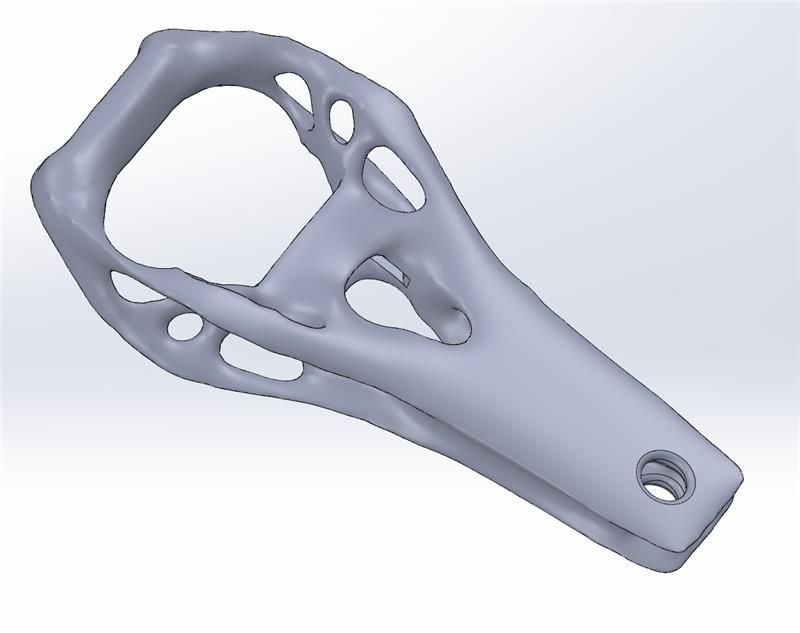
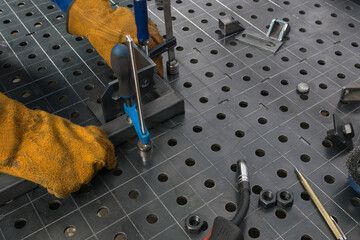
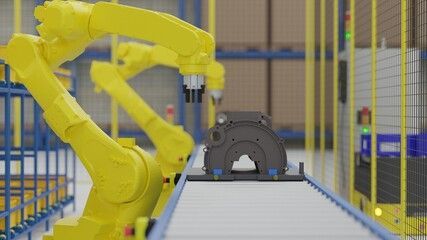
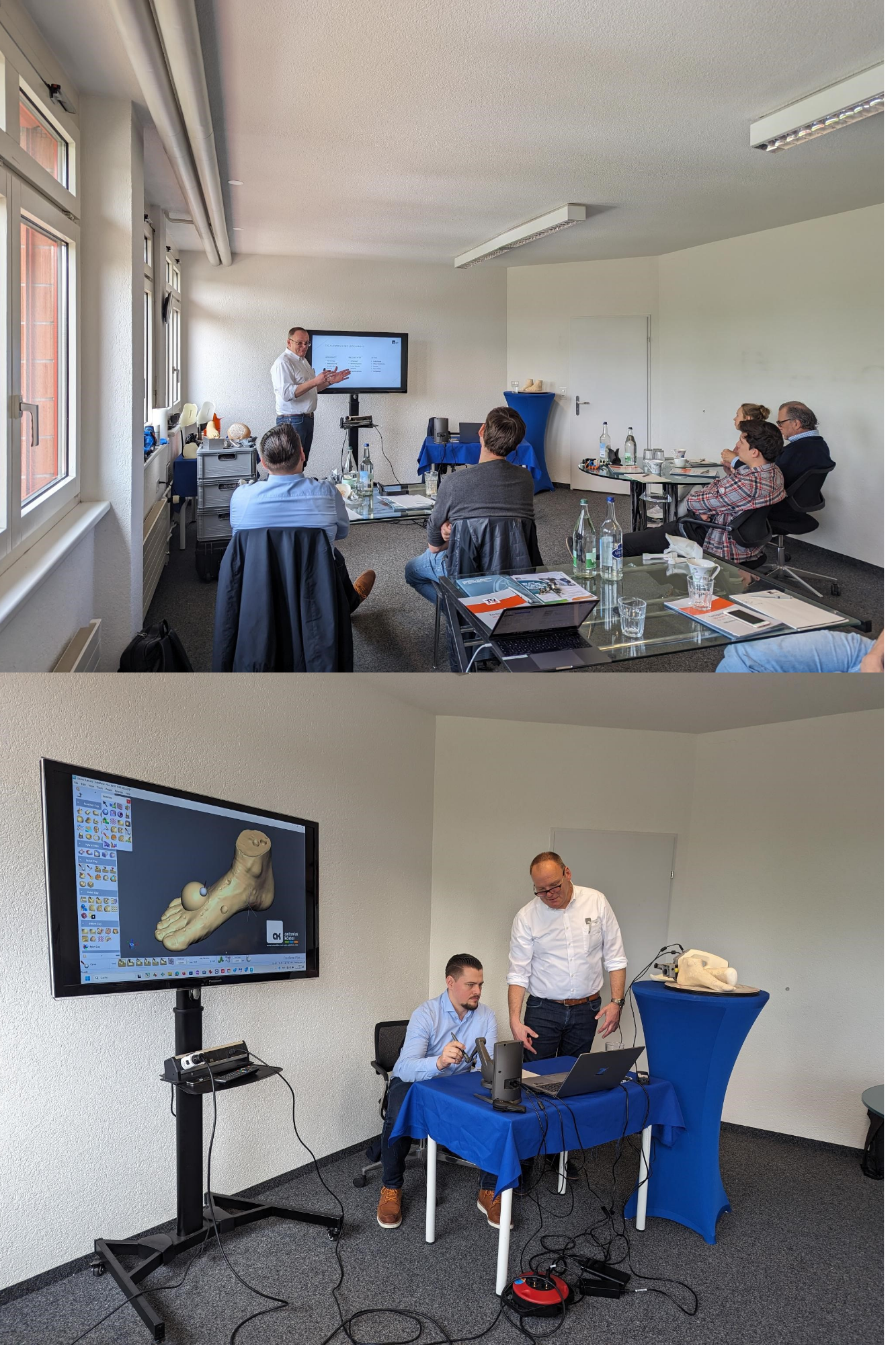
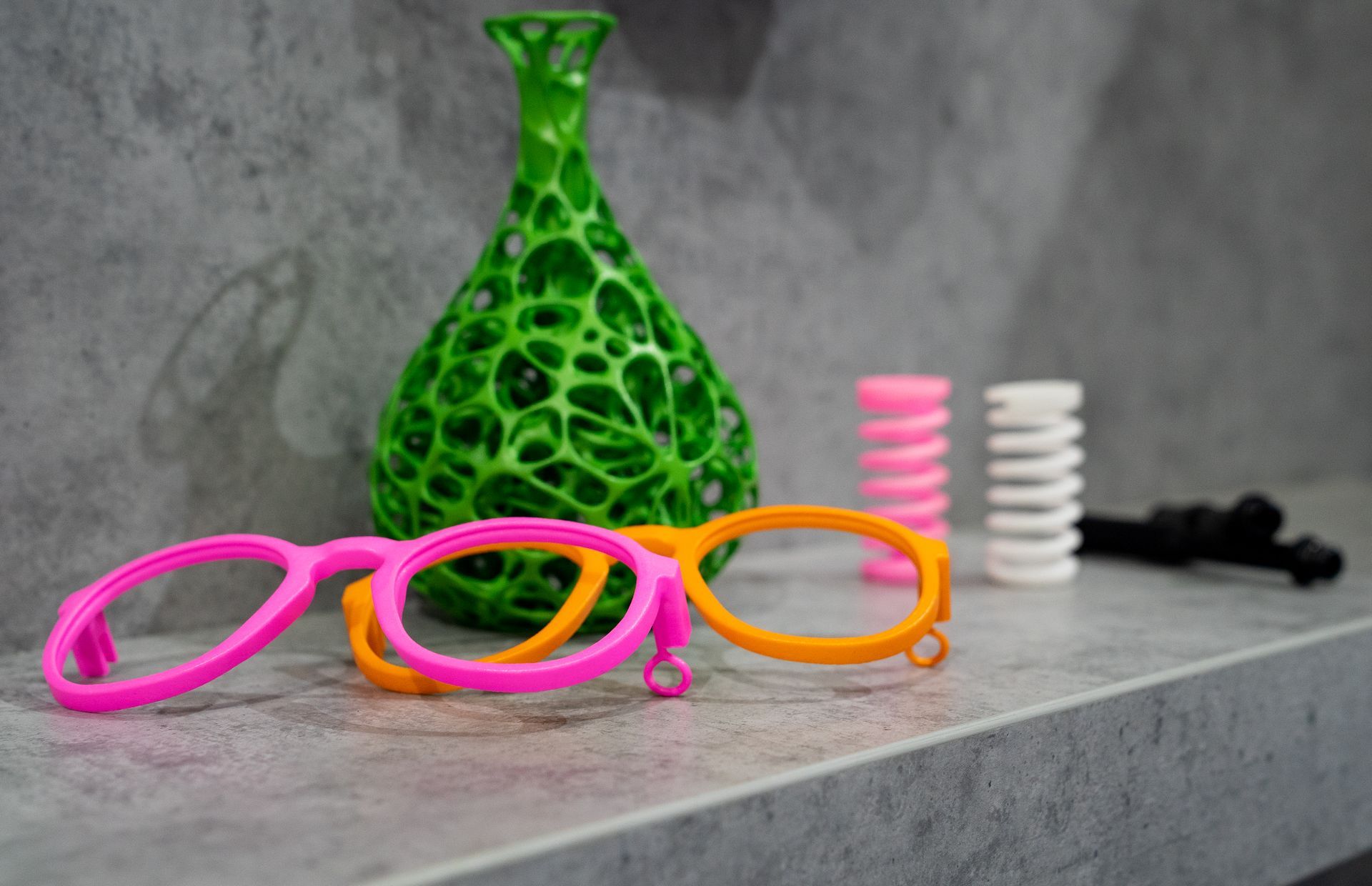